Key Takeaways
- Regular pipeline cleaning prevents blockages and maintains flow efficiency.
- Advanced technologies like intelligent pigging and robotics enhance cleaning effectiveness.
- Eco-friendly cleaning methods contribute to environmental sustainability.
- Predictive maintenance strategies reduce downtime and operational costs.
Table of Contents
- Understanding Pipeline Contamination
- Traditional Cleaning Methods
- Innovative Cleaning Technologies
- Implementing Effective Cleaning Strategies
Understanding Pipeline Contamination
Contamination in pipelines can lead to serious challenges in modern infrastructure, from reduced efficiency to safety hazards and costly repairs. Debris, corrosion, moisture, and chemical residue can accumulate over time, affecting the quality of transported materials and compromising the integrity of the pipeline system. If not addressed, these issues can disrupt operations and shorten the lifespan of critical infrastructure components.
Routine inspection and internal cleaning are essential to managing these risks. Specialized tools are used to remove buildup and detect problem areas before they escalate. One such tool is the super pig, a high-performance device designed to clean and inspect pipelines more effectively than traditional methods. By using advanced technology to detect irregularities and clear out contaminants, this approach supports the safe and efficient function of pipelines in a variety of industrial applications.
Traditional Cleaning Methods
For many decades, industries have depended on a core set of established techniques to maintain the cleanliness and reliability of their pipelines. Among the most prominent are:
- Mechanical Pigging: This process employs specially engineered devices known as “pigs”—rigid or flexible objects inserted into the pipeline and propelled by the flow of fluid or by mechanical means. As these pigs travel through the system, they physically scrape away deposits, scale, and other debris clinging to the walls, restoring flow capacity and mitigating build-up.
- Chemical Cleaning: In scenarios where mechanical means alone cannot dislodge stubborn contaminants, chemical cleaning agents are introduced. These carefully selected chemicals break down tough deposits, dissolve rust, and help to inhibit or reverse corrosion. While powerful, these chemicals must be chosen and handled carefully to avoid damaging the pipeline or causing unwanted chemical reactions.
- Hydraulic Flushing: Another widely used technique, hydraulic flushing relies on high-velocity water or other fluid forced through the system under significant pressure. This strong flow dislodges and carries away loose debris, sediment, and other material that mechanical pigs may leave behind.
While these time-tested methods have served the industry well, they have inherent limitations and risks. Mechanical and chemical cleaning can generate waste that must be carefully disposed of to prevent environmental damage, and using harsh chemicals raises safety concerns for workers and local ecosystems. Although less invasive, hydraulic flushing may be less effective against hardened deposits or biofilms. Importantly, all these approaches often require that pipeline operations be temporarily halted, leading to downtime that affects productivity and profitability. As regulatory demands, environmental awareness, and operational pressures increase, industries are increasingly motivated to adopt cleaner, brighter, and more sustainable methods.
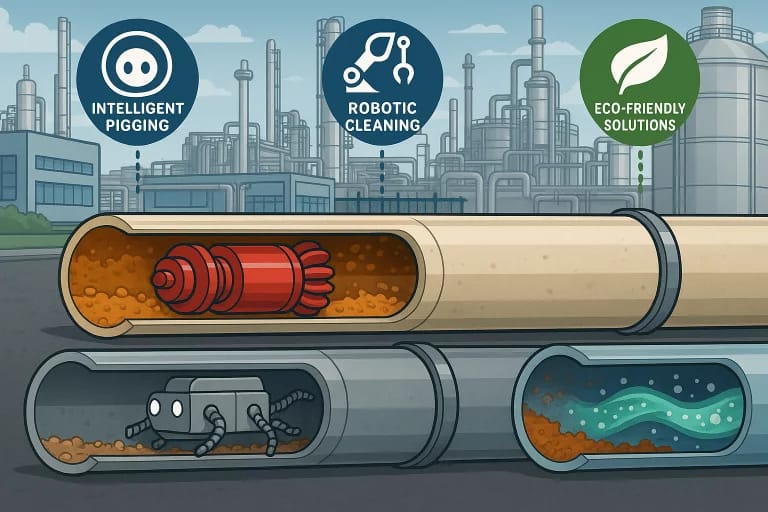
Innovative Cleaning Technologies
Modern demands for cleanliness, efficiency, and sustainability have catalyzed technological innovation in pipeline cleaning. The industry has turned to advanced tools and methods that overcome the limits of traditional practices and contribute to long-term performance, safety, and environmental responsibility. These solutions allow for thorough cleaning and continuous monitoring while optimizing the balance between performance and eco-friendly operations.
Intelligent Pigging
The evolution of pipeline pigging technology has led to “intelligent pigs”—advanced devices that clean pipes while capturing high-resolution data on wall thickness, corrosion, and anomalies. By transmitting this information in real-time without system shutdowns, they enable proactive maintenance strategies that extend pipeline lifespan and reduce risks of leaks and failures. This early detection minimizes costly surprises and lowers emergency repairs, benefiting safety and efficiency.
Robotic Inspection and Cleaning
Robotic technologies are revolutionizing pipeline maintenance by enabling advanced systems to navigate complex and hard-to-reach piping. These robots, equipped with cameras, sensors, and cleaning tools, can be remotely operated or work autonomously. They enhance safety by minimizing human involvement in hazardous areas, such as toxic or underground pipelines. Additionally, robotic cleaners quickly adapt to changing conditions, identify problems in real-time, and provide detailed maintenance records.
Eco-Friendly Cleaning Solutions
As awareness of environmental impact increases, pipeline cleaning technologies focus on sustainability. Companies opt for biodegradable, non-toxic, and water-based agents instead of harmful chemicals. Solar-powered pumps and battery-driven robots are also rising, reducing carbon footprints and supporting sustainability goals. By choosing eco-friendly solutions, industries can improve corporate responsibility and regulatory compliance.
Implementing Effective Cleaning Strategies
Implementing an efficient and effective pipeline cleaning program is neither a one-size-fits-all process nor a single event; it requires thoughtful planning, continuous data analysis, and ongoing adjustments tailored to evolving operational needs and goals. A step-by-step, data-driven framework ensures an optimal balance between cleaning frequency, downtime, cost, and risk mitigation.
- Assessment: A systematic evaluation involves comprehensive inspections and historical data analysis to identify contaminants and their scale, allowing targeted cleaning measures.
- Technology Selection: Based on the assessment, decision-makers choose suitable cleaning technologies. Factors include pipe material, contaminant nature, operational impact, and environmental considerations.
- Execution: Cleaning follows strict protocols, prioritizing in-situ methods to minimize disruption while achieving effective results.
- Monitoring: Digital monitoring systems are integrated during and after cleaning to track performance, detect recurring issues, and ensure regulatory compliance.
- Maintenance Planning: Predictive maintenance uses analysis from inspections and cleaning to forecast intervention needs, reducing emergency repairs and maximizing operational uptime.
Must Read: How Regular Maintenance Prevents Common Commercial Roof Problems